آینده صنعت خودروسازی به فیبر کربن وابسته است
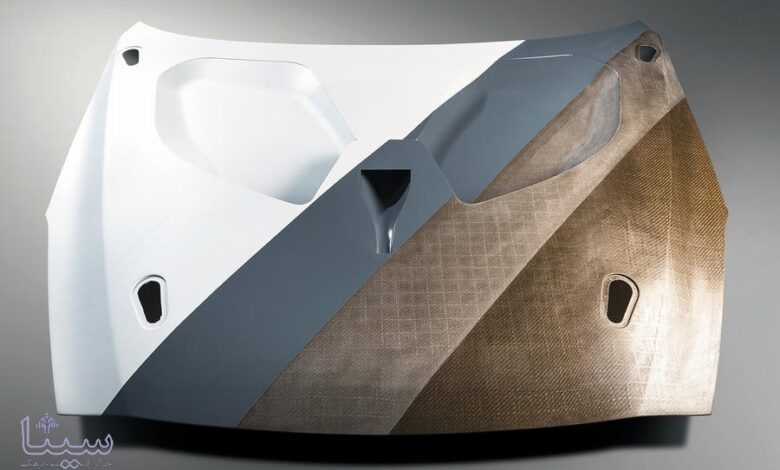
به گزارش سیناپرس، صنعت کامپوزیت به سمت راه حل های مقرون به صرفه تر حرکت می کند و یکی از جدید ترین آنها نوع جدیدی از روش قالب گیری فشرده است که توسط گروه Retrac، متخصص کامپوزیت و تامین کننده قطعات ماشین های فرمول ۱ توسعه یافته است. این رویکرد جدید قالب گیری فشرده با استفاده از الیاف طبیعی گیاهی و الیاف کربن بازیافتی و همچنین ترکیب رزینهای زیستی است.
روش سنتی ساخت اجزای کامپوزیتی، از جمله مخازن خودروهای فورمول ۱، به این صورت است که بافتهای مختلفی از حصیر فیبر کربنی از قبل آغشته به رزین را در یک قالب قرار می دهند و سپس کل قسمت را در کیسه خلاء قرار داده تا فشرده شود و در نهایت آن را در اتوکلاو با فشار شش بار در دمای ۲۰۰ درجه سانتیگراد به مدت چهار تا شش ساعت می پزند. انجام این کار مقدار زیادی انرژی مصرف کرده و گران تمام می شود.
به گزارش sinapres،جایگزین های استفاده از اتوکلاو یا دیگ های صنعتی پخت فیبر کربن، شامل قالب گیری انتقال رزین است که در آن مواد در قالب گذاشته می شوند. هنگامی که قالب بسته می شود رزین تزریق شده و مخلوط فشرده و گرم می شود. گفتنی است پیش از این لامبورگینی نسخه قالب گیری انتقال رزین خود را در سال ۲۰۱۱ توسعه داد که RTM-Lambo نامیده می شود.
به گزارش سیناپرس، نسخه قالب گیری فشرده با افزودن ماده مات کننده خشک به قالب شروع شده و به دنبال آن قبل از اینکه ترکیب فشرده و گرم شود، رزین با این ترکیب مخلوط می شود. این روش ارزان تر از روش سنتی است زیرا در مرحله ساخت، بخش آغشته کردن ماده مات کننده با رزین را نداشته و می تواند به استفاده از کامپوزیتهای زیستی برای مخاطبان وسیع تری کمک کند. مهم این است که کل فرآیند در یک مرحله تکمیل می شود و به جای ساعت ها، چند دقیقه طول می کشد.
اگرچه قالب گیری فشرده سازی شده قبلاً برای بعضی قطعات توسط برخی از تولید کنندگان و تامین کنندگان پیشرو اتخاذ شده است اما سیستم Retrac از این جهت متفاوت است که پرس ۶۰ تنی برای کنترل دقیق تر پرس به جای هیدرولیک توسط نوع خاصی از موتورهای الکتریکی هدایت می شود. بر خلاف هیدرولیک که در کل چرخه فشرده سازی انرژی مصرف می کند، این موتورها فقط با بسته شدن پرس انرژی مصرف می کنند.
به گزارش سیناپرس، دستگاه پرس فوق دارای سیستم خلاء داخلی است که توسط نرم افزار کنترل می شود و این امکان را به وجود می آورد تا قطعات فیبر کربنی سریع تر و با استاندارد و کیفیت بالا ساخته شوند تا با استفاده از الیاف و رزین های طبیعی به کیفیت قابل قبولی دست یابند.
به گفته سازندگان، رزین های زیستی استفاده شده دارای بالاترین نسبت مواد پایدار در بازار هستند. به دلیل کیفیت و سرعت فرآیند، ساخت دهها هزار قطعه در سال امکان پذیر خواهد بود و انتظار می رود که قطعات کامپوزیتی برای تعداد بیشتری از سازندگان خودرو در دسترس باشد.
مترجم : محسن فلاحی پناه
منبع: autocar