یافتههای جدید محققان ایرانی برای بهبود مقاومت کامپوزیت سرامیکی
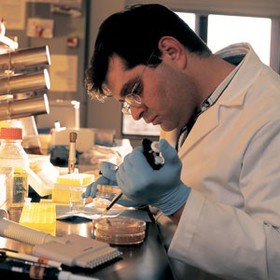
به گزارش ایسنا، شهره لرستانی، فارغالتحصیل کارشناسی ارشد رشته مواد سرامیک و مجری طرح با بیان این که دوغابهای سیلیسیم- کاربید سیلیسیم (Si/Sic) برای ساخت کامپوزیت نیترید سیلیسیم – کاربید سیلیسیم جهت استفاده در ساخت قطعاتی که مقاومت سایشی و خمشی بالایی دارند، استفاده میشود، گفت: تقویت مواد سرامیکی غیراکسیدی با استفاده از فیبرها و فازهای سوزنی شکل میتواند به بهبود خواص مکانیکی مانند استحکام و میزان حساسیت سطحی و بالاتر رفتن مقاومت شوک حرارتی منتهی شود.
وی با بیان اینکه یک راه جهت رسیدن به این هدف، ساخت کامپوزیت است، افزود: یکی از کامپوزیتهای سرامیکی که دارای استحکام، مقاومت سایشی و مقاومت دما بالای مناسبی است، کامپوزیت نیترید سیلیسیم –کاربید سیلیسیم (Sic/Si3N4) است.
این پژوهشگر با اشاره به اینکه یک روش مقرون به صرفه که امروزه در جهان برای ساخت سرامیکهای مهندسی و کامپوزیتهای آنها مورد استفاده قرار میگیرد، روش ریختهگری دوغابی است، خاطرنشان کرد: ویژگیهای یک کامپوزیت ساخته شده به روش ریختهگری دوغابی که به طور عمده توسط ریزساختار و سطح مشترک فاز تقویتکننده و زمینه کنترل میشود، با خواص جریانی دوغابهای تهیه شده از آن نسبت مستقیم دارد.
وی ادامه داد: در این کار پژوهشی، از پودر کاربید سیلیسیم در دو دانهبندی متفاوت و پودر سیلیسیم استفاده شد. رفتار پخشپذیری دوغاب دارای مخلوط پودرهای سیلیسیم (Si) و کاربید سیلیسیم (Sic) در محیط آبی، توسط مطالعه رسوبگذاری به صورت تابعی از pH، اندازه گیری بررسی شد.
لرستانی افزود: در مرحله بعد، ساخت دوغاب با نسبتهای مختلفی از درصد وزنی آب به ماده جامد و درصد وزنی پودر سیلیسیم به کاربید سیلیسیم و درصدهای مختلفی از بالکلی و تایرون به عنوان مواد افزودنی جهت پراکندگی بیشتر در محدوده 7=pH و سپس بررسی ویژگیهای رئولوژی توسط رئومتر چرخشی و در پایان ریختهگری دوغاب دارای مخلوط پودرهای سیلیسیم و کاربید سیلیسیم در قالب گچی است.
وی گفت: پس از خروج قطعه از قالب و قرار دادن قطعه در خشککن، سینتر نمونهها در دماهای 1400، 1450 و 1490 درجه سانتیگراد در کوره اتمسفر کنترل شد و تحت فشار گاز نیتروژن به مدت دو ساعت انجام گرفت که در نتیجه، پس از طی این فرآیند کامپوزیت نیترید سیلیسیم –کاربید سیلیسیم ساخته میشود.
مجری طرح در خصوص نتایج این بررسی گفت: پس از بررسی مطالعات مربوط به خواص رئولوژی و ویژگیهای بدنههای سینتر شده مشخص شد که بهترین دوغاب مربوط به دوغاب با غلظت 70 درصد وزنی ماده جامد و شامل مخلوط پودرهای سیلیسیم و کاربید سیلیسیم با نسبت 30 به 70 و نیز پنج درصد وزنی بالکلی و 0.5 درصد وزنی تایرون و بهترین دما به جهت داشتن مطلوبترین نتیجه از نظر چگالی، درصد تخلخل و استحکام دمای 1450 درجه سانتیگراد بوده است. تحولات فازی، ریزساختار و مورفولوژی قطعه سینتر شده به وسیله میکروسکوپ الکترونی روبشی و پراش پرتو ایکس صورت گرفت.
بر اساس این گزارش، این طرح با راهنمایی دکتر اسماعیل صلاحی و دکتر ایمان مباشرپور در پژوهشگاه مواد و انرژی انجام شده است.
No tags for this post.